Heat treatment Equipment
Specification:
Max depth:30m
Max width:12.8m
Max height:8m
Item | Specification | Qty |
台车式燃气热处理炉 Gas heat treatment furnace | Max size:30×12.8×8m | 12 sets |
加热炉 Heating furnace | Max size: 12×3.5×2.8m | 6 sets |
退火炉 Annealing furnace | Max size: 16.5×4×3m | 6 sets |
Stock ASTMA29 4130/30CrMo Hot Rolled Steel Round Bar Bright Bar, AISI 4130 Round Bar, AISI 4130 Rods, 4130 alloy steel flat bar alloy steel bar stock Suppliers and Dealer in China
AISI 4130 Round Bar Specifications | ||
Dimensions | : | EN, DIN, JIS, ASTM, BS, ASME, AISI |
Size | : | 5 mm To 500 mm |
Diameter | : | 0.1 mm to 100 mm |
Length | : | 100 mm To 3000 mm Long & Above |
Finish | : | Black, Bright Polished, Rough Turned, NO.4 Finish, Matt Finish, BA Finish |
Tolerance | : | H8, H9, H10, H11, H12, H13K9, K10, K11, K12 or as per clients’ requirements |
Form | : | Round, Square, Hex (A/F), Rectangle, Billet, Ingot, Forging Etc. |
4130 AISI Round Bar Chemical Composition
Grade | C | Mn | Si | P | S | Fe | Mo | Ni | Cr |
AISI 4130 | 0.28-0.33 | 0.40-0.60 | 0.15-0.35 | 0.035 max | 0.025 MAX | 97.3-98.22 | 0.15-0.25 | 0.50 max | 0.80-1.10 |
AISI 4130 Rods Mechanical Properties
Density | Melting Point | Tensile Strength | Yield Strength (0.2%Offset) | Elongation |
7.85 g/cm3 | 1432 ℃ | 560 | 460 | 21.50% |
Equivalent Grades for 4130 AISI Round Bar
STANDARD | WERKSTOFF NR. | UNS | JIS | BS | EN |
AISI 4130 | 1.7218 | G41300 | JIS G4105 | BS 970 | 25CrMo4 |
AISI 4130 Round Bar Application Industries
- Off-Shore Oil Drilling Companies
- Power Generation
- Petrochemicals
- Gas Processing
- Specialty Chemicals
- Pharmaceuticals
- Pharmaceutical Equipment
- Chemical Equipment
- Sea Water Equipment
- Heat Exchangers
- Condensers
- Pulp and Paper Industry
4130 AISI Rods Test Certificates
EN 10204/3.1B,
AISI 4130 Rods Packaging


Where to buy carbon steel bar stock A519 AISI1045/CK45 Hot rolled mechanical bar from Wuxi xingye special steel company
Description Name: ASME SA519 / ASTM A519 GR.1045 boiler pipes, A519 pipes, Grade 1045 ASTM A519 carbon steel tube, ASTM A519 GR. 1045 mechanical pipes, ASTM A 519 GR.1045 carbon steel pipe, Grade 1045 SEAMLESS PIPE, ASTM A519 Grade 1045 cold drawn seamless steel tubes, ASTM A519 Gr.1045 pipes and tubing, ASTM A519 SAE1045 seamless tubing, alloy steel tube, carbon steel tube, mechanical tubing, Seamless steel tube, steel tube.
Size: 10mm-323.8mm
Schedule: 10-XXS / Thk
Shape: Round or Special sections.
Length: Single random length/ Double random length or as customer’s actual request
Grade: SAE 1045 / GRADE 1045 / AISI 1045
Condition: The purchaser shall specify a sizing method
Thermal Treatments:
A-Annealed,
N– Normalized,
QT-Quenched and Tempered,
SR-Stress Relieved or Finished Anneal.
ASTM A519 SAE1045 seamless tubing Chemical Composition (%):
Grade | C | Mn | P≤ | S≤ |
1045 | 0.43-0.50 | 0.60-0.90 | 0.040 | 0.050 |
No surface finish, beveled ends ↓ ↓ ↓
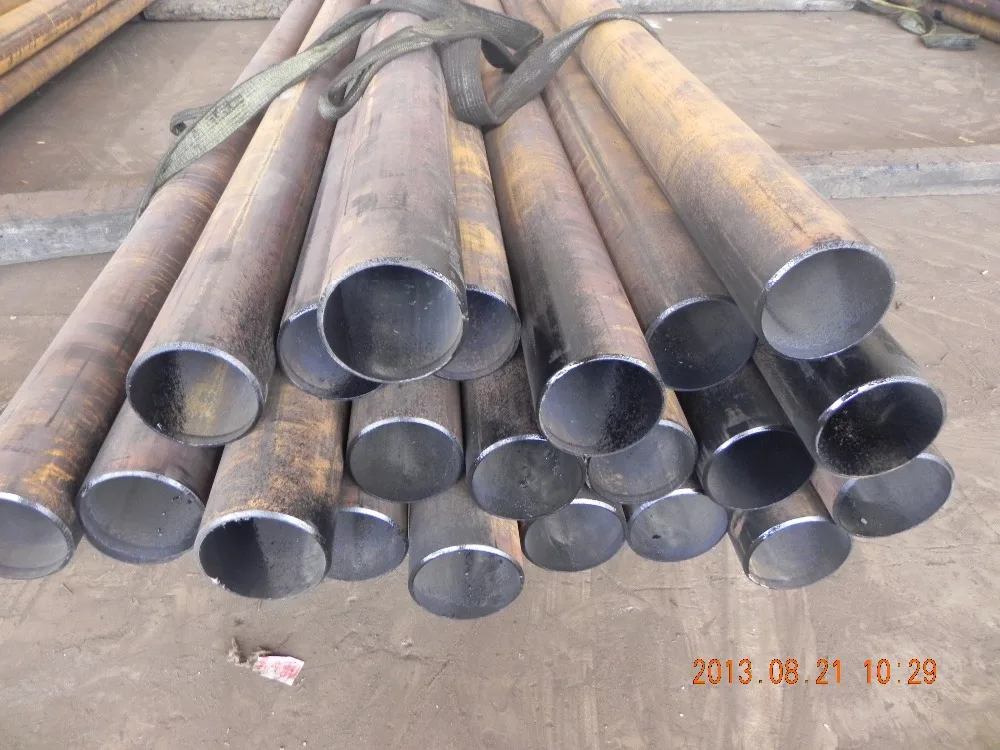
NO surface finish, plain
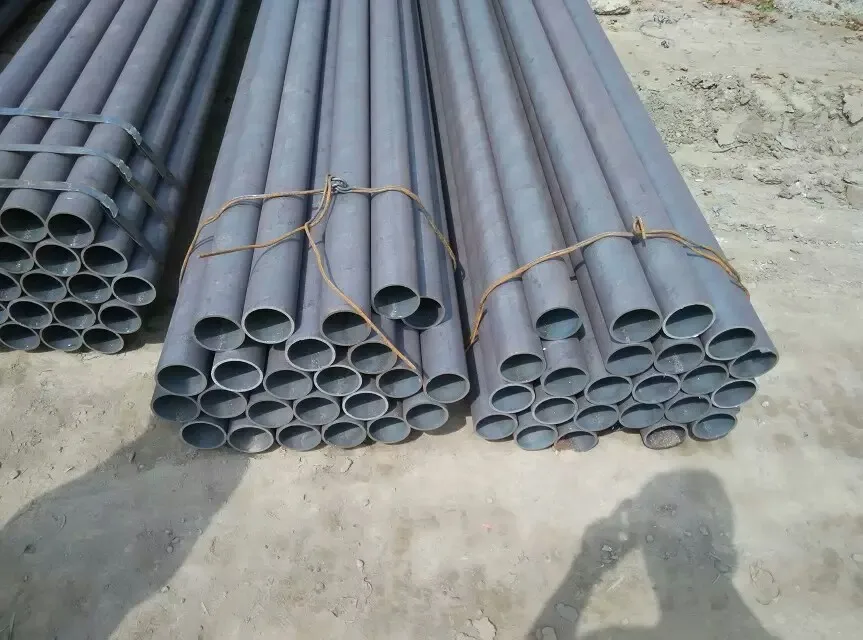
Package:
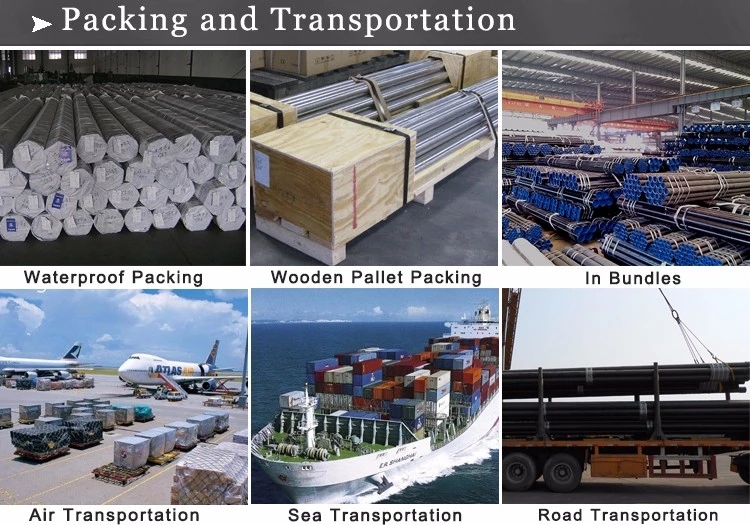
Stock 100CrMn6/1.3520 Chromium-manganese alloy bearing steel
Applications
Roller bearings with thickness up to 50 mm.
Description
Medium alloy, oil-hardening tooling steel, which is hard-wearing.
Quality Standard:
DIN 17230-1980 Ball and Roller Bearing Steels
Chemical Composition(%)
C | Si | Mn | P | S | Cr | Ni | Cu |
---|---|---|---|---|---|---|---|
0.90-1.05 | 0.50-0.70 | 1.00-1.20 | 0.030 max | 0.025 max | 1.40-1.65 | 0.30 max | 0.30 max |
HEAT TREATMENT:
Soft Annealing
Heat to 760-800oC, cool slowly in furnace. This will produce a maximum Brinell hardness of 217.
Normalizing
Normalizing temperature: 860-900oC.
Stress Relieving
Stress relieving to remove machining stresses should be carried out by heating to approx. 650oC, holding for 1-2 hours at heat, followed by air cooling. This operation is performed to reduce distortion during heat treatment.
Hardening
Harden from a temperature of 830-890oC followed by oil quenching. Hardness after quenching is approx. 64 HRC.
Tempering
Tempering temperature: 150-180oC.
Forging
Hot forming temperature: 1100-850oC.
Stock Alloy solid bar 1.8509/38CrMoAl/905M39/SACM645/41CrAlMo7 Q+T with bright surface condition
1. Chemical composition
Grade | C | Si | Mn | P | S | Cr | Mo | Al |
38CrMoAl | 0.35-0.42 | 0.20-0.45 | 0.30-0.60 | ≤0.035 | ≤0.035 | 1.35-1.65 | 0.15-0.25 | 0.70-1.10 |
2. Equivalent Steel Grade
GB | ASTM | DIN |
38CrMoAl | 7140 | 1.8509 |
3. Applications:
1
2.For parts of larger cross-sections, crankshafts, gears and so on.
4.Main features:
1.Good resistance to tempering.
2.Excellent corrosion resistance.
3.Excellent dimensional stability during heat treatment.
4.Excellent polishing
5.Good wear resistance
Case Hardening Steels A1444 42CrMo4/En19/4140 alloy steel bar stock high tensile steel for bolts alloy steel bright bar manufacturer
what is high tensile steel bar
Application:
4140 Alloy Steel/SAE 4140 Steel
Chemical Composition
C | Si | Mn | Cr | Mo | P | S |
0.38-0.43 | 0.40max | 0.60-0.90 | 0.90-1.20 | 0.15-0.30 | ≤0.035 | ≤0.035 |
how high tensile steel is made Heat treatment
Forging | Heat to 1150°C. Hold until uniform. Minimum forging temperature 850°C.Cool slowly in ashes or sand etc. |
Annealing | Heat to 830°C-850°C.Cool in furnace. |
Normalising | Heat to 870°C-900°C.Cool in still air. |
Stress Relieving | Annealed: Heat to 600°C-650°C.Hardened: Heat to 500°C-550°C.Cool in still air. |
Hardening | Heat to 830°C-880°C. Quench in oil or polymer. |
Tempering | Heat to 450°C-700°C cool in still air. NB. Tempering within the range 200°C-420°C will result in temper brittleness and should be avoided. |
Mechanical Properties:
Tensile Strength (Mpa) | Yield Strength (Mpa) | Hardness (HB) | Elongation (%) | Izod Impact (J) |
850-1000 | 665 min | 248-302 | 13 min | 54 min |
UT:100% U.T acc. to ASTM AS 1065 -Level 2
Surface condition
Black surface/ Grinded/ Machined |
Package: wooden case & water proof.
Transport:
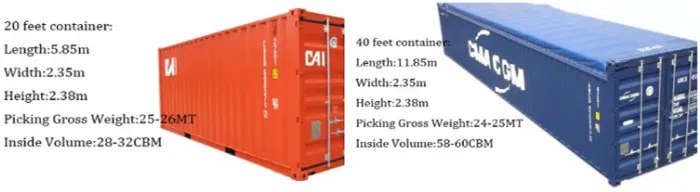

Cheap price Alloy 4140/SCM440/42CrMo4 Cold Drawn Bar Precision from China mill
Yeguang steel Metal is a distributor of 4140 grade cold drawn steel bar. 4140 bars have high hardenability, and the molybdenum content provides high strength and uniformity of hardness. Unlike other grades, the carbon content of
4140 Mechanical Properties (Annealed)
Tensile Strength | 95,000 psi |
Yield Strength | 60,500 psi |
Elongation in 2″ | 25.7% |
Reduction of Area | 55.9% |
Brinelle Hardness | 197 |
4140 Mechanical Properties (Normalized)
Tensile Strength | 148,000 psi |
Yield Strength | 95,000 psi |
Elongation in 2″ | 17.7% |
Reduction of Area | 46.8% |
Brinelle Hardness | 302 |
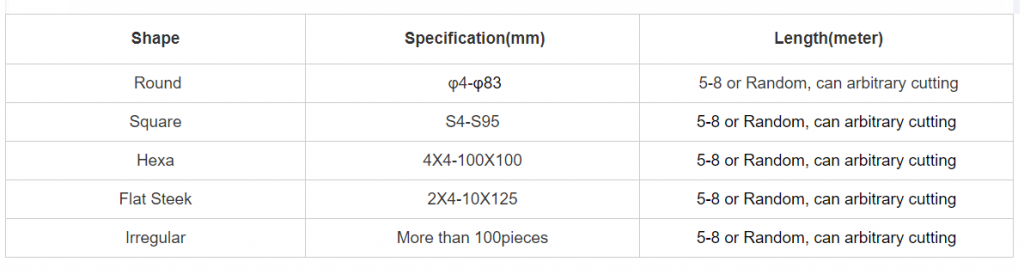
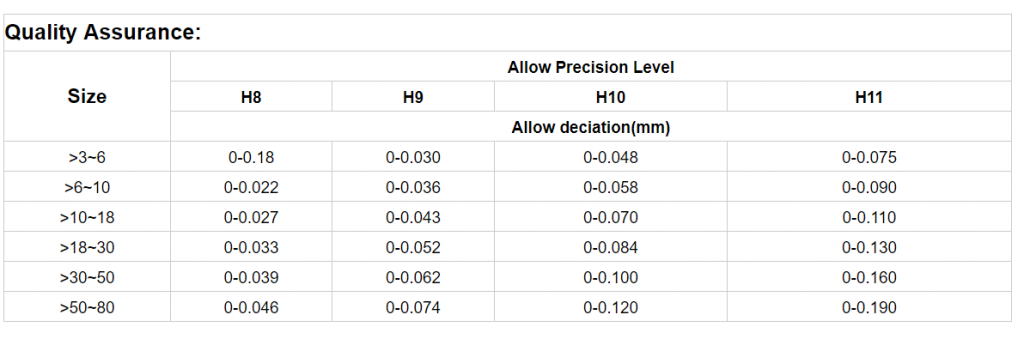
Chemcial Compositions(%): | |||||||||
Quality Standard | Steel Grade | C | Si | Mn | P | S | Cr | Ni | Mo |
ASTM A29 | 4140 | 0.38-0.43 | 0.15-0.35 | 0.75-1.00 | ≤0.035 | ≤0.040 | 0.80-1.10 | / | 0.15-0.25 |
JIS G4053 | SCM440 | 0.38-0.43 | 0.15-0.35 | 0.60-0.90 | ≤0.030 | ≤0.030 | 0.90-1.20 | ≤0.25 | 0.15-0.30 |
EN 10083-3 | 42CrMo4 | 0.38-0.45 | ≤0.40 | 0.60-0.90 | ≤0.025 | ≤0.035 | 0.90-1.20 | 0.15-0.30 | / |
- ASTM A29 Standard Specification Steel Bars Carbon and Alloy Hot Wrought General Requirements
- JIS G4053 2008 Low alloyed steels for machine structural use
- Steel for quenching and tempering-Part3: Technical delivery conditions for alloy steels of EN 10083-3:2007
Steel Grades
- ASTM A29: 4140
- JIS G4053: SCM440
- EN10083: 42CrMo4
Surface Condition:
- Smooth Surface
Grinded Surface- Peeled Surface
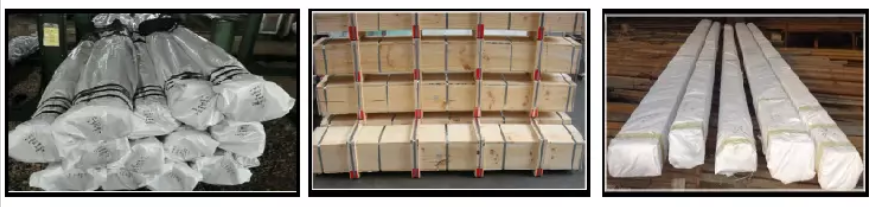
ASTM A681 H13 AISI H13/DIN 1.2344/JIS SKD61 Machining Tool Steel Round Bar Best Price Per Kg Pound
Applications:
H13 tool steels are suitable for forming extrusion dies.
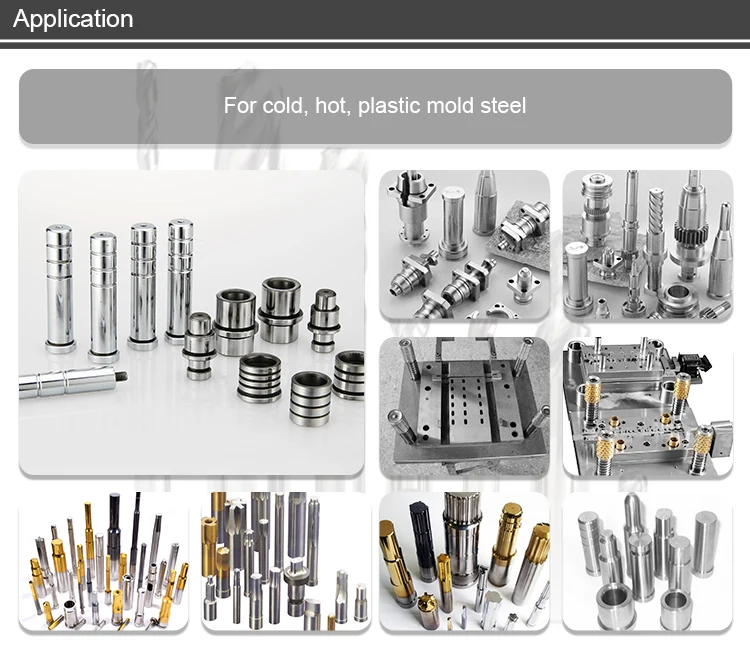
Steel Machining:
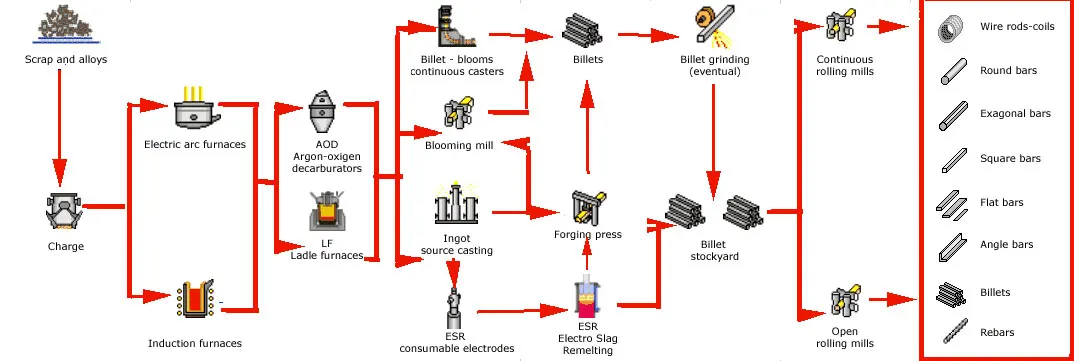
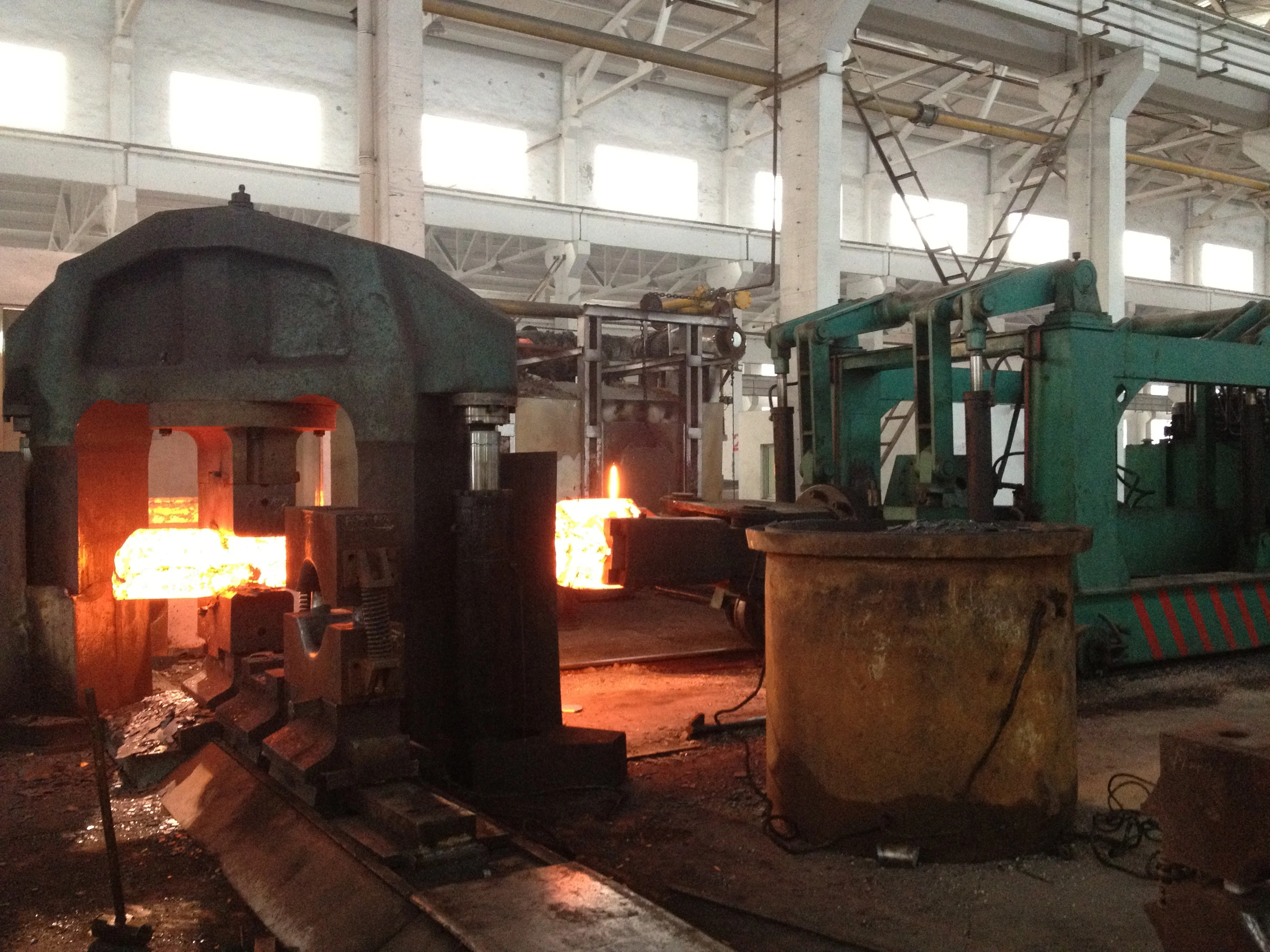
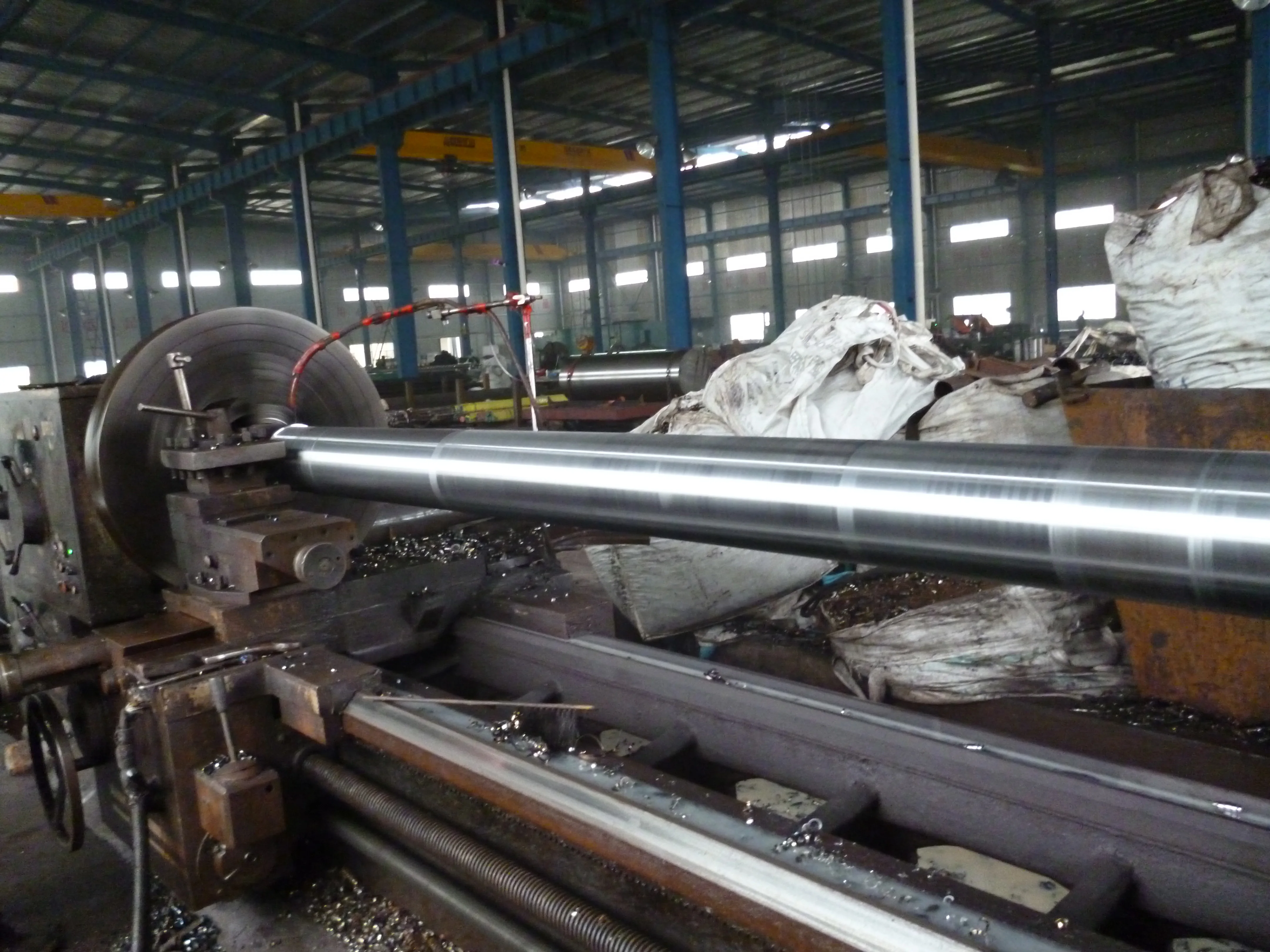
Chemical composition(%)
Grade | C | Mn | P Max | S Max | Si | Cr | V | Mo |
H13 Alloy tool steel | 0.32 to 0.45 | 0.20 to 0.60 | 0.030 | 0.030 | 0.80-1.25 | 4.75 to 5.50 | 0.80to 1.20 | 1.10 to 1.75 |
Grade | C | Mn | P | S | Si | Cr | V | Mo |
1.2344 | 0.32-0.45 | 0.20-0.60 | 0.030max | 0.030max | 0.80-1.25 | 4.75-5.5 | 0.80-1.2 | 1.10-1.75 |
Hardeness
Type | Annealed Max BHN | Cold Drawn MaxBHN |
H13 | 235 | 262 |
Steel Grade | AISI H13/DIN 1.2344/JIS SKD61 |
Size & Dimension | Diameter: 600 mm(Max) |
Surface treatment | Black/Peeling/Polishing/Machined |
HBW | ≤235 |
Technique | Cold/Hot rolled, Cold-Drawn or Hot Forged |
Heat Treatment | Annealed; Quenched; Tempered |
Delivery Condition | Hot Rolled or Forged/Peeled or Black Surface/Annealed or QT |
Test | SGS/UT100%/Elements Testing |
Certificate | ISO/Mill Certificate |
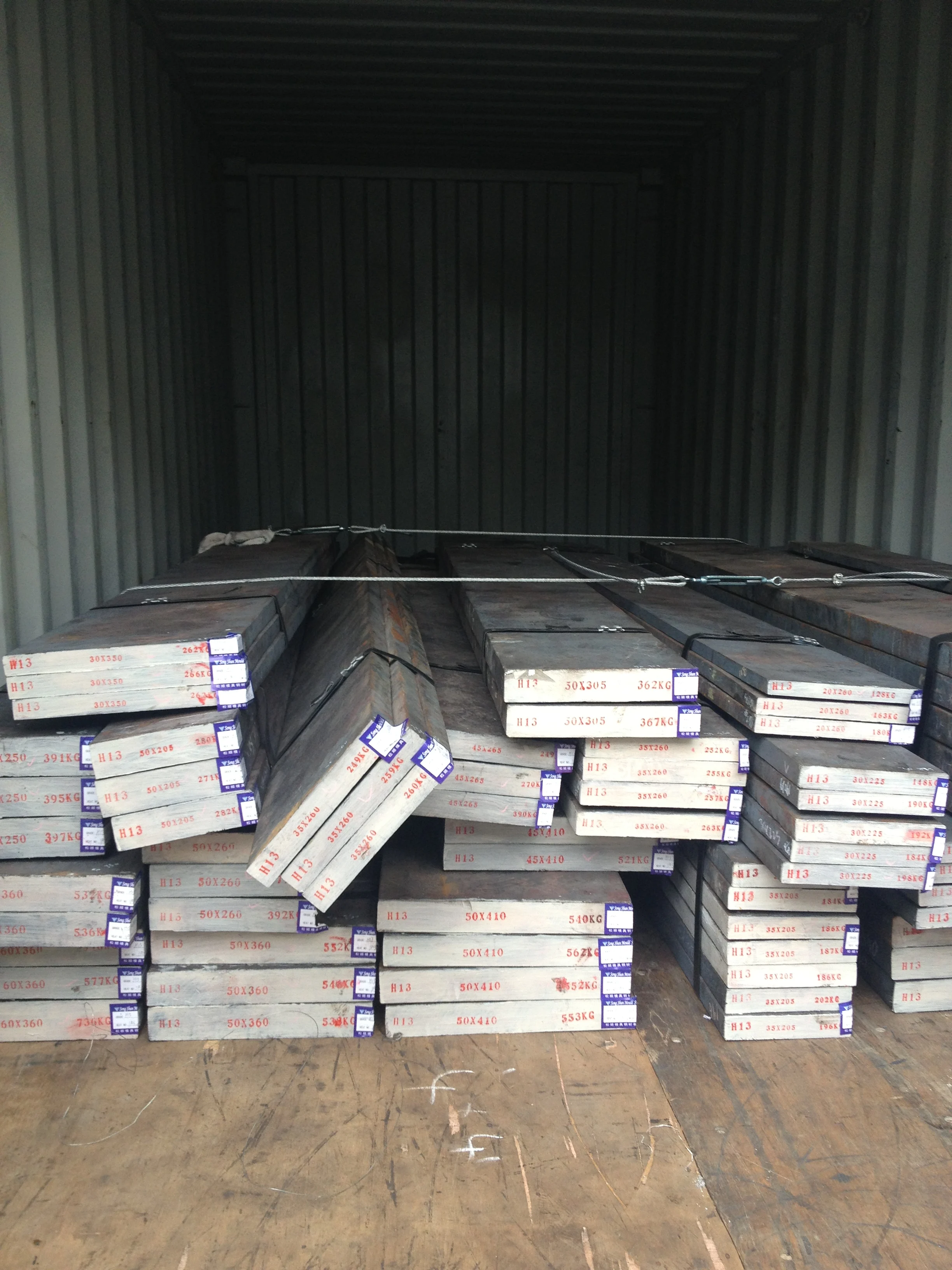
CUSTOMER FEEDBACK
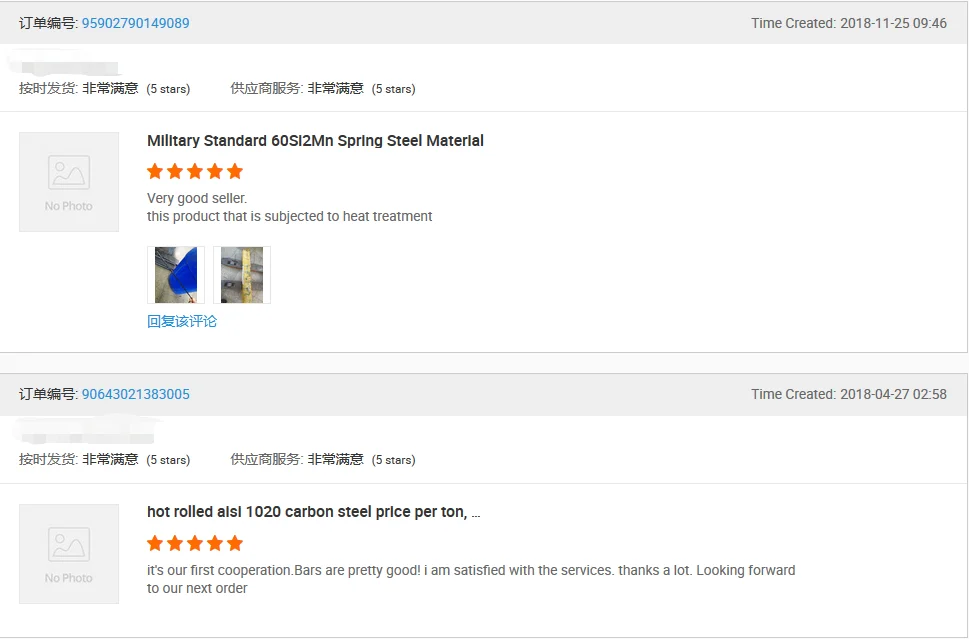
Stockist Structural Alloy Steel 1.6582 34CrNiMo6 EN24 Round Bar
Application:
High voltage bolts and nuts, crankshafts, camshafts, transmission axles, torsion bars, drive shafts, pump shafts, worm shafts, conveyor rollers, stems, pins, tie rods, clutch discs. Large-mass dies for hot stamping.1.6582 Steel is widely used in the aerospace industry for structural parts of flaps assembly, fuselage and landing gear, propeller plane axles.
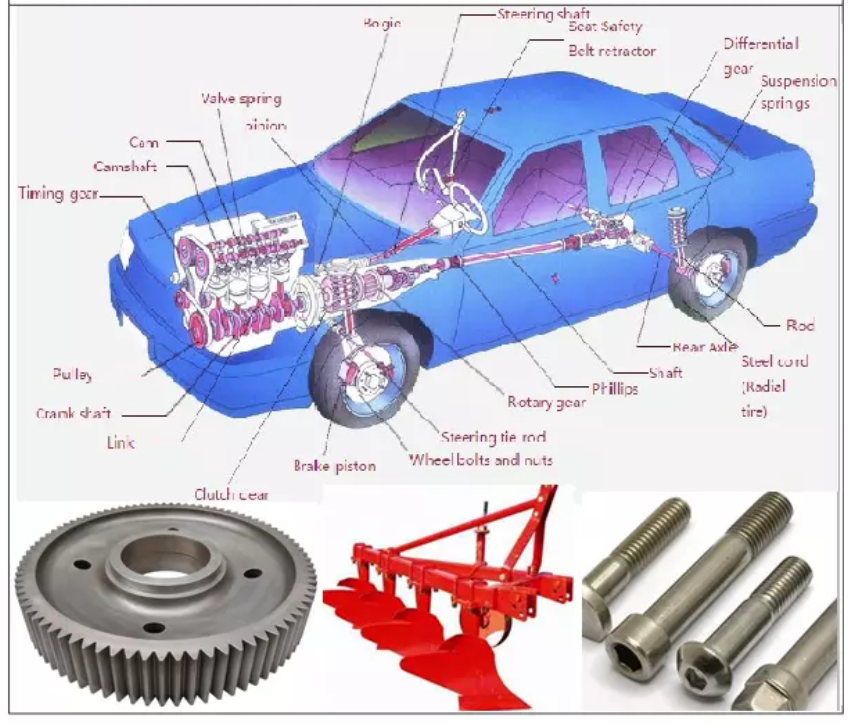
Product Description:
1.6582 Steel is a heat treatable, low alloy steel containing nickel, chromium and molybdenum. It is known for its toughness and capability of developing high strength in the heat treated condition while retaining good fatigue strength. A very popular, versatile steel. It can be heat-treated to produce a wide range of tensile strength in moderate sections.
>>>Steel Grades
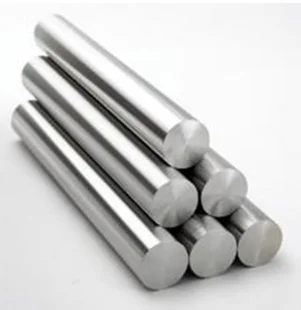
DIN1.6582,
SNCM439,
35NCD6,
38Ch2N2MA,
EN24,
817M40,
34CrNiMo6,
Standard: En10083
Heat Treatment:
Annealing: Heat to 800℃ – 850 ℃ , hold until temperature is uniform throughout the section and cool in furnace.
Flame or Induction Hardening: 1.6582steel can be further surface hardened by either the flame or induction hardening methods resulting in a case hardness in excess of Rc 50. Parts should be heated as quickly as possible to the austenitic temperature range (830℃ – 860℃ ) and required case depth followed by an immediate oil or water quench, depending upon hardness required, workpiece size/shape and quenching arrangements. Following quenching to hand warm, most components should be tempered between 150℃ – 200℃ to remove quenching stresses in the case. This will have little effect on case hardness.
Hardening: Heat to 830℃ – 860℃, hold until temperature is uniform throughout the section, soak for 10 – 15 minutes per 25 mm section, and quench in oil, water, or polymer as required.
*Temper immediately while still hand warm.
Nitriding: 1.6582 steel can also be successfully nitrided, giving a surface hardness of up to Rc 60. Nitriding is carried out at 490℃– 530℃, followed by slow cooling (no quench) reducing the problem of distortion. Parts can therefore be machined to near final size, leaving a grinding allowance only. The tensile strength of the core is usually not affected since the nitriding temperature range is generally below the original tempering temperature employed. N.B. Nickel is inert to the action of nitrogen and in general resists its diffusion into steel. This can result in lower case hardness or longer nitriding cycle times for steels containing nickel such as 1.6582 steel.
Stress Relieving: Heat to 600℃– 650 ℃, hold until temperature is uniform throughout the section, soak for 1 hour per 25 mm of section, and cool in still air.
Tempering: Re-heat to 450℃– 660℃as required, hold until temperature is uniform throughout the section, soak for 1 hour per 25 mm of section, and cool in still air. N.B. Tempering should be avoided if possible within the range 250℃ – 450℃ due to temper brittleness.
Notes on Heat Treatment: Heating temperatures, rate of heating, cooling and soaking times will vary due to factors such as work piece size/shape also furnace type employed, quenching medium and work piece transfer facilities etc.
Chemcial composition:
Grade | C | Mn | P | S | Si | Cr | Ni | Mo |
1.6582 | 0.30-0.38 | 0.50-0.80 | 0.025max | 0.035max | 0.40max | 1.30-1.70 | 1.30-1.70 | 0.15-0.30 |
Packing details | In seaworthy packing, as your requirement. |
Delivery details | within 10-50 days |
Mill′s test certificate:
EN 10204/3.1 with all relevant data reg. chem. composition, mech. properties and results of testing.