Materials:carbon steel, alloy steel, stainless steel, super-alloy, aluminum alloy, titanium alloy Products:flange, tube, gear blank, slewing blank, casing
Out-diameter: rang from 27 to 354 inches
Max weighing: 85000 pounds
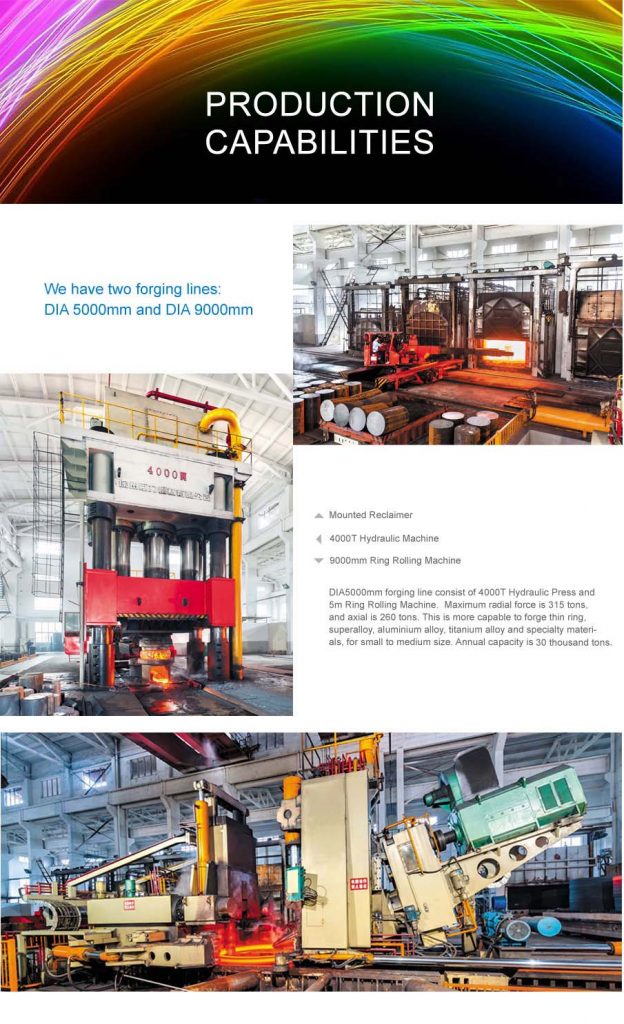
Wuxi Xingye Group Steel Co., Ltd
Manufacturer of hot rolled alloy & carbon QT round bar
Materials:carbon steel, alloy steel, stainless steel, super-alloy, aluminum alloy, titanium alloy Products:flange, tube, gear blank, slewing blank, casing
Out-diameter: rang from 27 to 354 inches
Max weighing: 85000 pounds
The applications of 36CrNiMo16 Steel are numerous and includes the following:
BS EN10250 Open die forging for general engineering purposes
ASTM A788 Standard Specification for Steel Forgings, General Requirements
EN | Material No. | BS | NF |
---|---|---|---|
36CrNiMo16 | 1.6773 | 835M30/EN30B | 35NCD16 |
C | Mn | Si | P | S | Cr | Ni | Mo |
---|---|---|---|---|---|---|---|
0.32-0.39 | 0.30-0.60 | 0.40 max | 0.030 max | 0.025 max | 1.60-2.00 | 3.60-4.10 | 0.25-0.45 |
Dia/Thickness(mm) | Tensile Strength Rm (Mpa) | Yield Strength R2 (Mpa) | Elongation (longitudinal direction) Al (%) | Elongation (transverse direction) At (%) | Impact properties (KV J) (longitudinal) | Impact properties (KV J) (transverse) |
---|---|---|---|---|---|---|
160 max | 1000 min | 800 min | 11 min | 8 min | 45 min | 22 min |
160-330 | 1000 min | 800 min | 11 min | 8 min | 45 min | 22 min |
330-660 | 1000 min | 800 min | 11 min | 8 min | 45 min | 22 min |
Heat Treatment:
Heat treatment temperatures, including rate of heating, cooling and soaking times will vary due to factors such as the shape and size of each EN30B steel component. Other considerations during the heat treatment process include the type of furnace, quenching medium and work piece transfer facilities. Please consult your heat treatment provider for full guidance on heat treatment of this 4.25% nickel alloy steel.
Forging | Heat the steel carefully to the forging temperature of 1000-1100°C, soak well. After forging, cool slowly in a furnace to 100°C maximum and anneal immediately. |
Annealing | To obtain the softest condition heat carefully to 630-650°C. Soak for a minimum of 2 hours, then cool in the furnace or in air. It is advisable to repeat this treatment to obtain the best machining characteristics. |
Stress Relieving | Where the machining operations have been severe, we recommend stress relieving EN30B alloy steel before finish machining and hardening. Heat carefully to 630-650°C then cool in the furnace or in still air. |
Hardening | Heat uniformly to 810-830°C and when thoroughly soaked at this temperature cool in air or quench in oil according to mass. Hardening from neutral salt baths will help to prevent scaling or decarburisation and is strongly recommended. Pre heat at 300-400°C, raise to the hardening temperature of 810-830°C, quench into salt standing at 300-320°C. Withdraw and cool in air. Alternatively, tools may be vacuum hardened. If desired, hardened and tempered tools can be cyanide hardened to give a shallow carburised case to die surfaces with increased hardness values up to Rockwell C56-60. Temper as soon as tools are hand-warm. |
Tempering | Re heat to the relevant tempering temperature. Soak for at least 2 hours per 25mm of Tempering °C 150 250 350 450 HRc 49 47 44 38 |
EN 10204/3.1 with all relevant data reg. chem. composition, mech. properties and results of testing.